Bend pipe fittings play a significant role in enhancing system scalability and expansion in piping systems. Here’s how they contribute:
- Routing Flexibility: Bend pipe fittings allow for changes in the direction of the piping system, enabling designers to route pipes around obstacles or through confined spaces. This flexibility facilitates the expansion of the system into new areas or the integration of additional equipment without the need for major structural modifications.
- Adaptation to Space Constraints: In situations where space is limited, such as in existing facilities or retrofit projects, bend pipe fittings provide a space-efficient solution for navigating around obstacles or fitting within tight confines. This adaptability allows for system expansion without requiring extensive changes to the existing layout.
- Ease of Installation: Bend pipe fittings can be easily installed in existing piping systems to accommodate expansions or modifications. Their simple design and compatibility with various piping materials make them a convenient choice for retrofitting or upgrading systems to meet increased demand or capacity requirements.
- Reduced Material and Labor Costs: By eliminating the need for custom bends or complex routing solutions, bend pipe fittings help reduce material costs associated with piping system expansion. Additionally, their ease of installation can result in lower labor costs compared to more intricate piping configurations.
- Minimized Disruption: When expanding or modifying a piping system, minimizing disruption to ongoing operations is essential. bend pipe fitting Bend pipe fittings enable modifications to be made with minimal downtime, as they can be quickly installed or integrated into existing systems without requiring extensive shutdowns or interruptions.
- Scalable Design: Piping systems designed with bend pipe fittings in mind are inherently scalable, allowing for future expansions or upgrades with minimal hassle. The modular nature of bend fittings enables system designers to plan for growth and accommodate changes in demand or capacity over time.
- Compatibility with Various Materials: Bend pipe fittings are available in a wide range of materials, including metal alloys, plastics, and composites. This compatibility allows for seamless integration with existing piping systems and facilitates the use of different materials to meet specific requirements or environmental conditions.
- Support for Complex Configurations: In applications where complex piping configurations are necessary, such as in industrial processes or utility distribution networks, bend pipe fittings provide the flexibility to create intricate layouts while maintaining system integrity and performance.
Overall, bend pipe fittings contribute to system scalability and expansion by providing routing flexibility, adaptation to space constraints, ease of installation, cost-effectiveness, minimized disruption, scalable design, compatibility with various materials, and support for complex configurations. These benefits make bend fittings a valuable component in the expansion and optimization of piping systems across a wide range of industries and applications.
How do bending black iron pipe address concerns regarding gas leakage and emissions?
Bending black iron pipe can address concerns regarding gas leakage and emissions in several ways:
- Seamless Construction: When black iron pipe is bent properly, it maintains its integrity and structural strength without compromising the integrity of the material. This seamless construction minimizes the risk of gas leakage at the bends, ensuring that the piping system remains airtight and leak-free.
- Proper Installation Techniques: Proper bending techniques, such as using mandrels or hydraulic benders, ensure that the pipe maintains its roundness and uniform thickness throughout the bend. This prevents weak spots or stress points that could potentially lead to gas leaks or emissions.
- Sealing Mechanisms: Bends in black iron pipe can be equipped with appropriate sealing mechanisms, such as threaded connections or compression fittings, to further enhance leak prevention. These sealing mechanisms create a tight and secure connection at the bends, minimizing the risk of gas leakage or emissions.
- Regular Inspection and Maintenance: Like any other component of a gas distribution system, bent black iron pipe should be subject to regular inspection and maintenance to ensure its integrity and reliability. bending black iron pipe Periodic checks for signs of corrosion, damage, or wear can help detect and address potential issues before they escalate into safety hazards.
- Material Durability: Black iron pipe is known for its durability and resistance to corrosion, making it a suitable choice for gas distribution systems. Properly bent black iron pipe can withstand the rigors of everyday use and environmental factors, minimizing the risk of deterioration or failure that could result in gas leakage or emissions.
- Compliance with Regulations: Bending black iron pipe in accordance with industry standards and regulatory requirements ensures that the piping system meets safety and environmental standards. Compliance with regulations governing gas distribution systems helps mitigate the risk of gas leakage and emissions, protecting both human health and the environment.
Overall, bending black iron pipe properly and employing appropriate installation techniques, sealing mechanisms, regular inspection, and compliance with regulations are essential measures to address concerns regarding gas leakage and emissions in gas distribution systems. By ensuring the integrity and reliability of the piping system, these measures help maintain safety and environmental compliance while minimizing the risk of potential hazards.
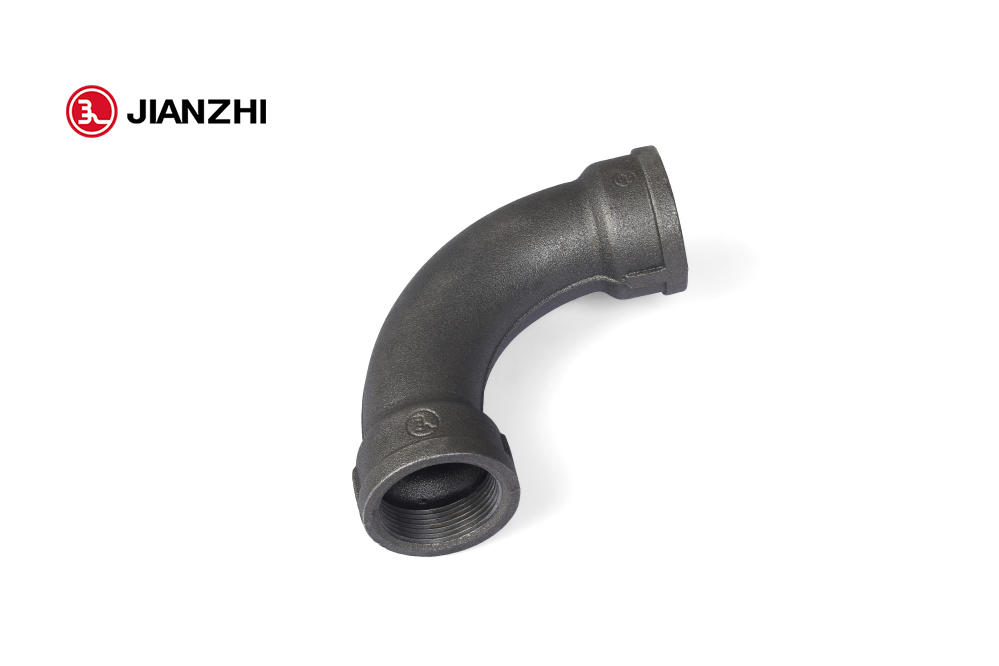