Proper alignment and calibration of the rotary axis attachment for cutting cylindrical or curved materials on a Fiber Laser Welding Machine are essential to achieve accurate and precise results.
Here are the steps operators can follow to ensure proper alignment and calibration:
- Check Rotary Axis Components: Inspect the rotary axis attachment components, including the chuck or clamping mechanism, tailstock, and rotary axis motor. Ensure that all components are securely mounted and properly aligned with the laser cutting head.
- Verify Chuck Alignment: If the rotary axis attachment uses a chuck to hold cylindrical or curved materials, verify that the chuck is aligned concentrically with the rotary axis motor shaft. Use precision measurement tools, such as dial indicators or laser alignment devices, to check for any misalignment and make adjustments as needed.
- Calibrate Rotary Axis Motor: Calibrate the rotary axis motor to ensure accurate rotation and positioning of cylindrical or curved materials. Use the machine’s control software to set the appropriate rotation speed and direction for the material being cut. Test the rotary axis motor’s movement to verify that it rotates smoothly and consistently.
- Check Tailstock Alignment: If the rotary axis attachment includes a tailstock for support, check that the tailstock is aligned parallel to the chuck or clamping mechanism. Ensure that the tailstock provides adequate support and does not introduce any deflection or misalignment during cutting operations.
- Test Cutting Accuracy: Perform test cuts on cylindrical or curved materials to verify the accuracy and precision of the rotary axis attachment. Fiber Laser Welding Machine Use geometric shapes or patterns to evaluate the cutting quality and dimensional accuracy of the cut parts. Make any necessary adjustments to the alignment or calibration of the rotary axis attachment based on the results of the test cuts.
- Fine-Tune Parameters: Adjust cutting parameters, such as laser power, cutting speed, and focus position, to optimize cutting performance for cylindrical or curved materials. Experiment with different parameter settings to achieve the desired cut quality and efficiency.
- Monitor Cutting Performance: Continuously monitor the cutting performance of the rotary axis attachment during production runs. Check for any signs of deviation or inconsistency in cut quality, dimensional accuracy, or material positioning. Make real-time adjustments to the alignment or calibration as needed to maintain optimal cutting performance.
- Regular Maintenance: Implement a regular maintenance schedule for the rotary axis attachment, including lubrication of moving parts, inspection of mechanical components, and cleaning of optical surfaces. Keep the attachment well-maintained to ensure reliable operation and longevity.
By following these steps and ensuring proper alignment and calibration of the rotary axis attachment, operators can achieve accurate and precise cutting of cylindrical or curved materials on the Fiber Laser Welding Machine. Proper alignment and calibration are essential for achieving high-quality results and maximizing productivity in laser cutting applications.
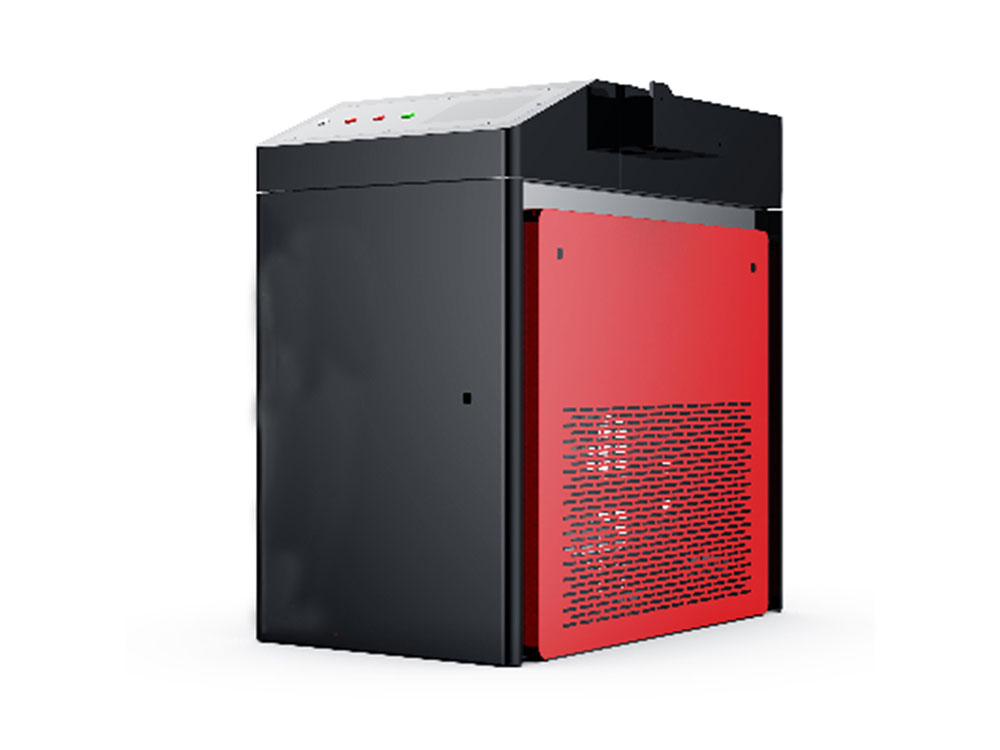