Conducting regular checks and maintenance on the electrical components of a Fiber Laser Cleaning Machine, including circuit boards, relays, and contactors, is essential to ensure the machine operates safely and reliably.
Here are the guidelines for conducting these checks and maintenance tasks:
- Visual Inspection: Perform a visual inspection of all electrical components, including circuit boards, relays, and contactors, to check for any signs of physical damage, such as cracks, corrosion, or burnt marks. Inspect wiring connections for signs of loose or damaged wires.
- Cleanliness: Keep the electrical components clean and free from dirt, dust, or debris that could affect their operation. Use a soft brush, compressed air, or a vacuum cleaner to remove dust and debris from circuit boards, relays, and contactors. Avoid using excessive force or abrasive materials that could damage delicate components.
- Tighten Connections: Check all wiring connections, terminal blocks, and screw terminals to ensure they are tight and secure. Loose connections can lead to overheating, arcing, or electrical faults. Use a torque screwdriver to tighten connections to the manufacturer’s specifications.
- Check for Overheating: Monitor the temperature of electrical components during operation to check for signs of overheating. Feel for hot spots or excessive heat buildup on circuit boards, relays, and contactors. Investigate any abnormalities and take corrective action, such as improving ventilation or reducing electrical load.
- Inspect Relays and Contactors: Inspect relays and contactors for signs of wear, damage, or arcing. Check the condition of contact points, Fiber Laser cleaning Machine terminals, and coils. Replace any relays or contactors that show signs of corrosion, pitting, or mechanical failure.
- Test Functionality: Test the functionality of relays and contactors by energizing and de-energizing them manually or using a multimeter. Verify that relays and contactors operate smoothly and that contacts make and break correctly without sticking or welding.
- Check Circuit Boards: Inspect circuit boards for signs of damage, such as burnt components, scorched traces, or blown fuses. Check for any loose components or solder joints. Use a magnifying glass or microscope to inspect components closely if necessary.
- Verify Voltage and Current: Use a multimeter or clamp meter to verify voltage and current levels at various points in the electrical system. Compare measured values to specifications provided by the manufacturer to ensure the system is operating within safe limits.
- Perform Software Updates: If the Fiber Laser Cleaning Machine is equipped with programmable logic controllers (PLCs) or electronic control systems, ensure that software updates or firmware upgrades are performed as recommended by the manufacturer. Follow proper procedures for installing updates to prevent data loss or system errors.
- Document Maintenance: Keep detailed records of all maintenance activities performed on the electrical components of the Fiber Laser Cleaning Machine. Document inspections, repairs, replacements, and any abnormalities observed during maintenance checks. This documentation helps track the history of maintenance and ensures compliance with safety regulations.
By following these guidelines for conducting regular checks and maintenance on the electrical components of the Fiber Laser Cleaning Machine, operators can help ensure safe and reliable operation of the equipment. Regular maintenance helps prevent electrical faults, reduces downtime, and extends the service life of the machine.
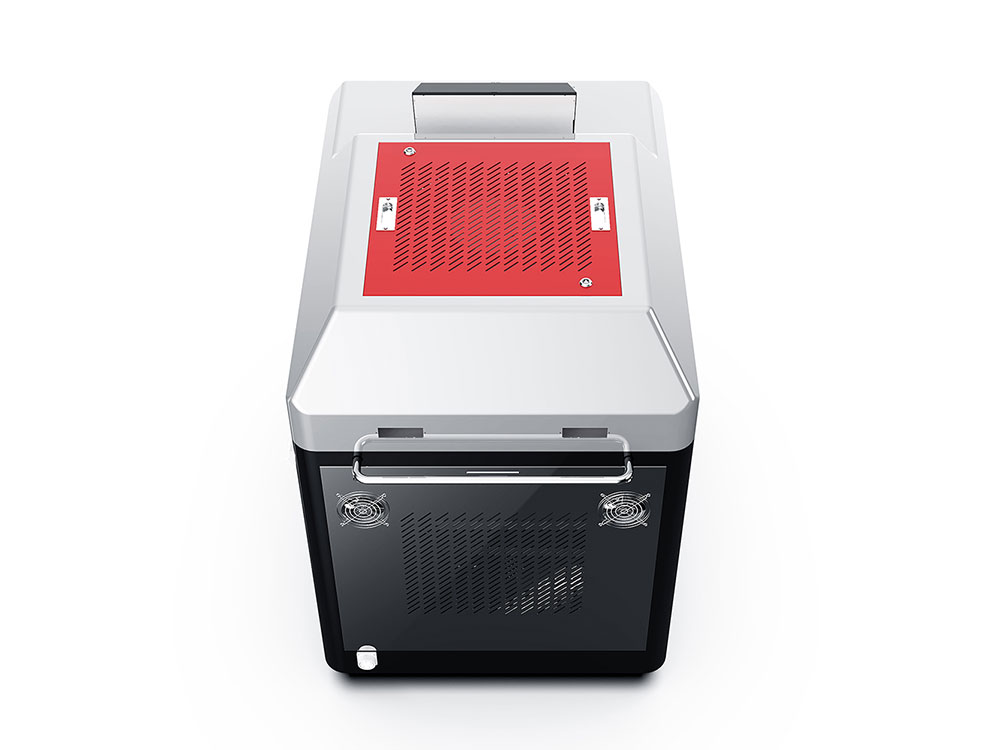